A friend gave me some live oak a while back, and while I’ve use smaller pieces for a few things, I had a fairly large chunk that I figured would make a bowl. It had bark inclusions and a few checks, and was generally pretty gnarly, but I mixed up some epoxy and red dye (too much red dye, based on the finished result) and filled and solidified the fragile bits, then turned this bowl.
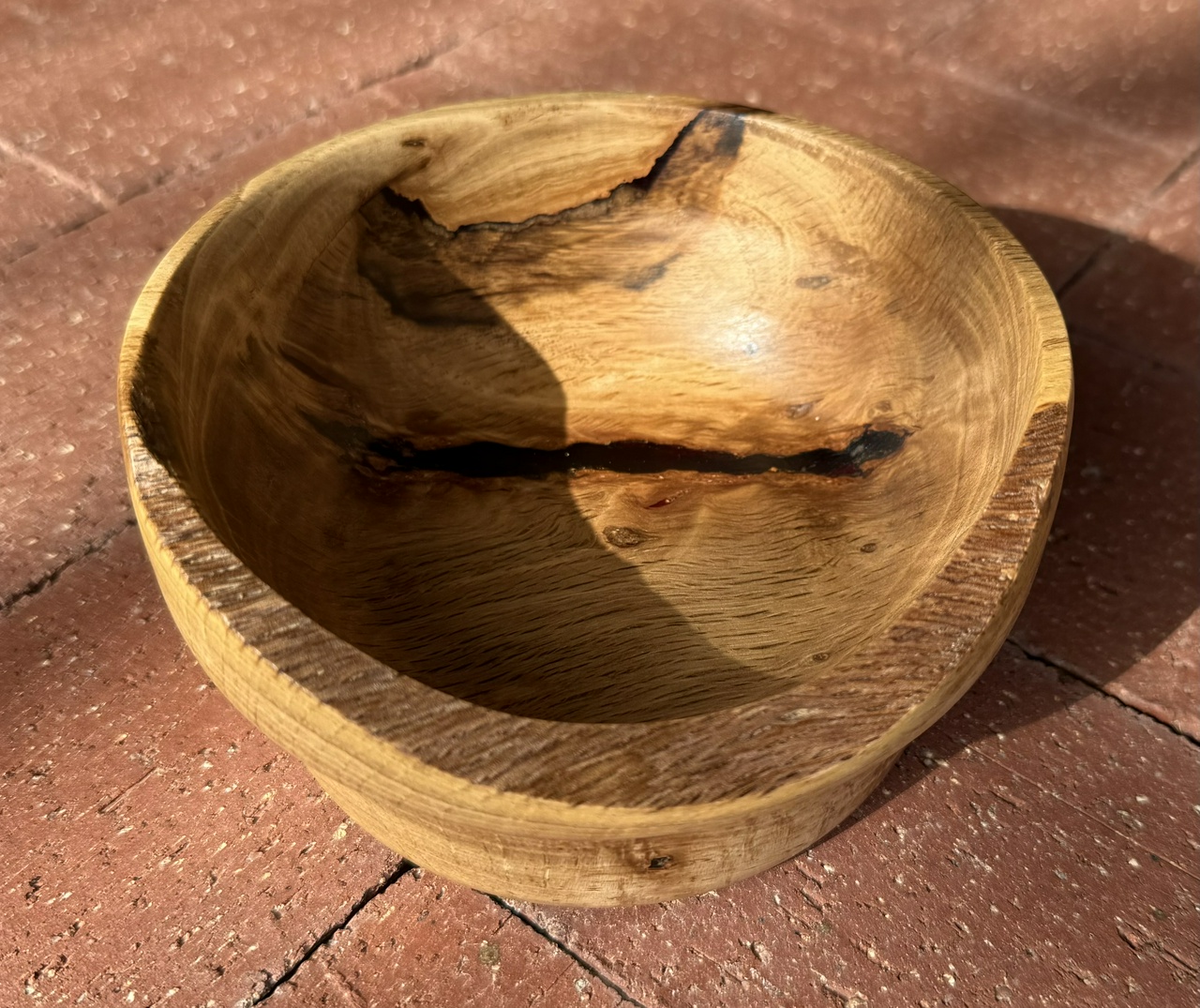
Read more...
I made a pair of boxes to hold pens recently. They're made with local wood, though I used some citrus from Arizona for accents. Both will be given away by a local non-profit at their anniversary celebration in October.
Read more...
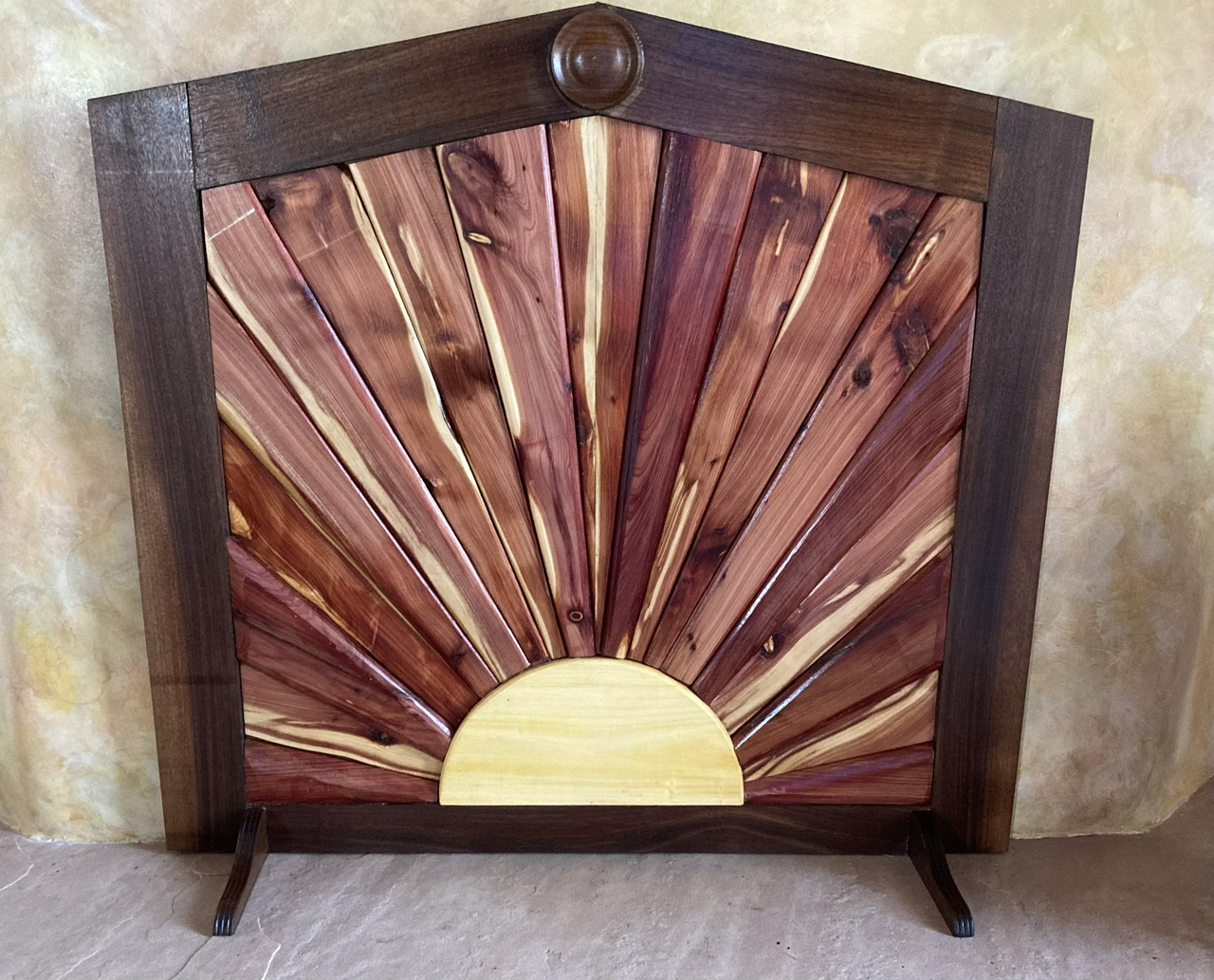
I built a screen for our fireplace recently, and am fairly happy with the result. The screen is for times when we’re not using the fireplace, since it looks dirty, and when the wind gusts, sometimes the damper blows open, and then we get a cold wind into the living room. This also greatly reduces the noise from wind blowing across the top of the chimney.
Read more...
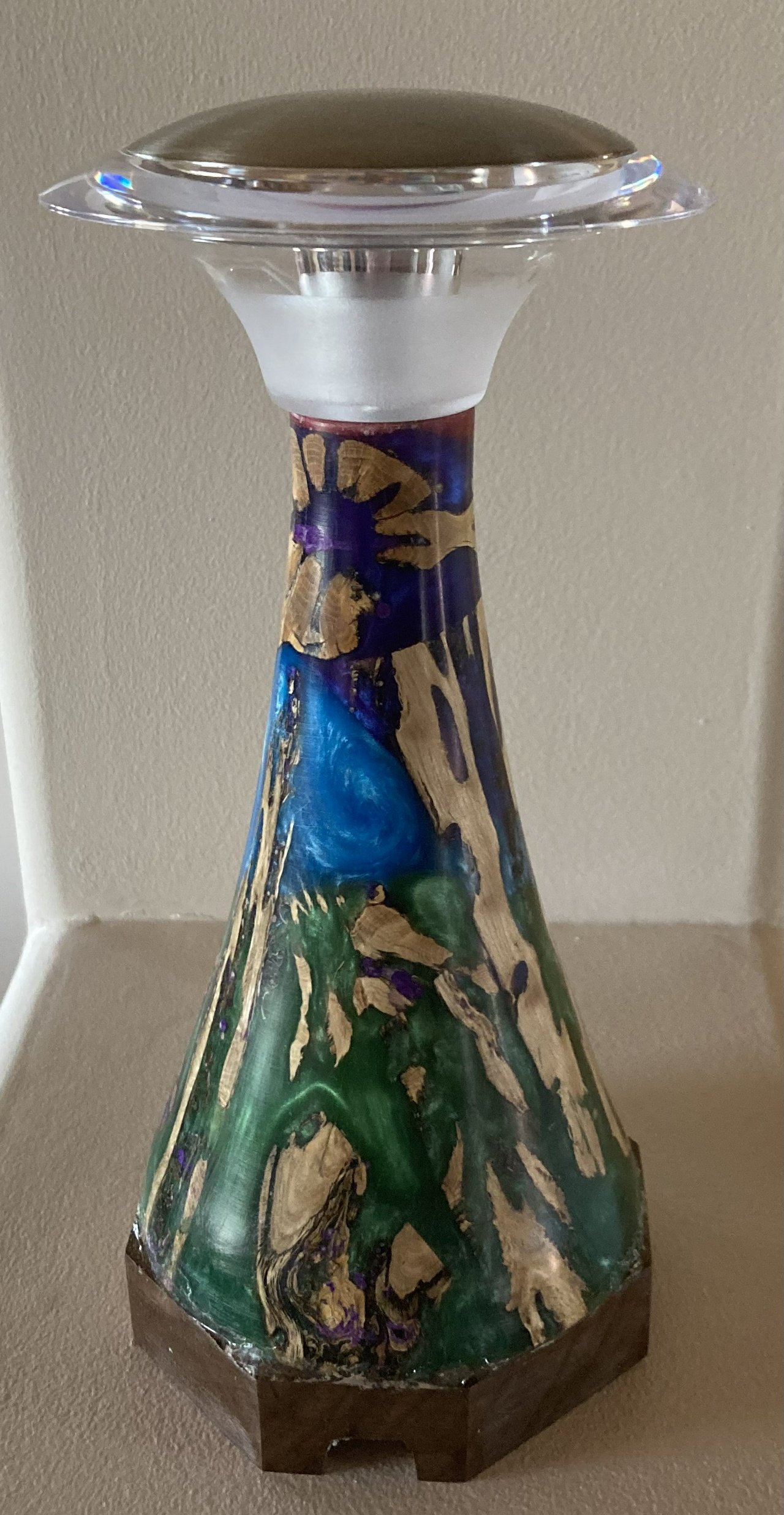
I finished another cholla and resin lamp this morning. Started pouring the resin for this in March or April, so it went somewhat quicker than previous lamps.
Read more...
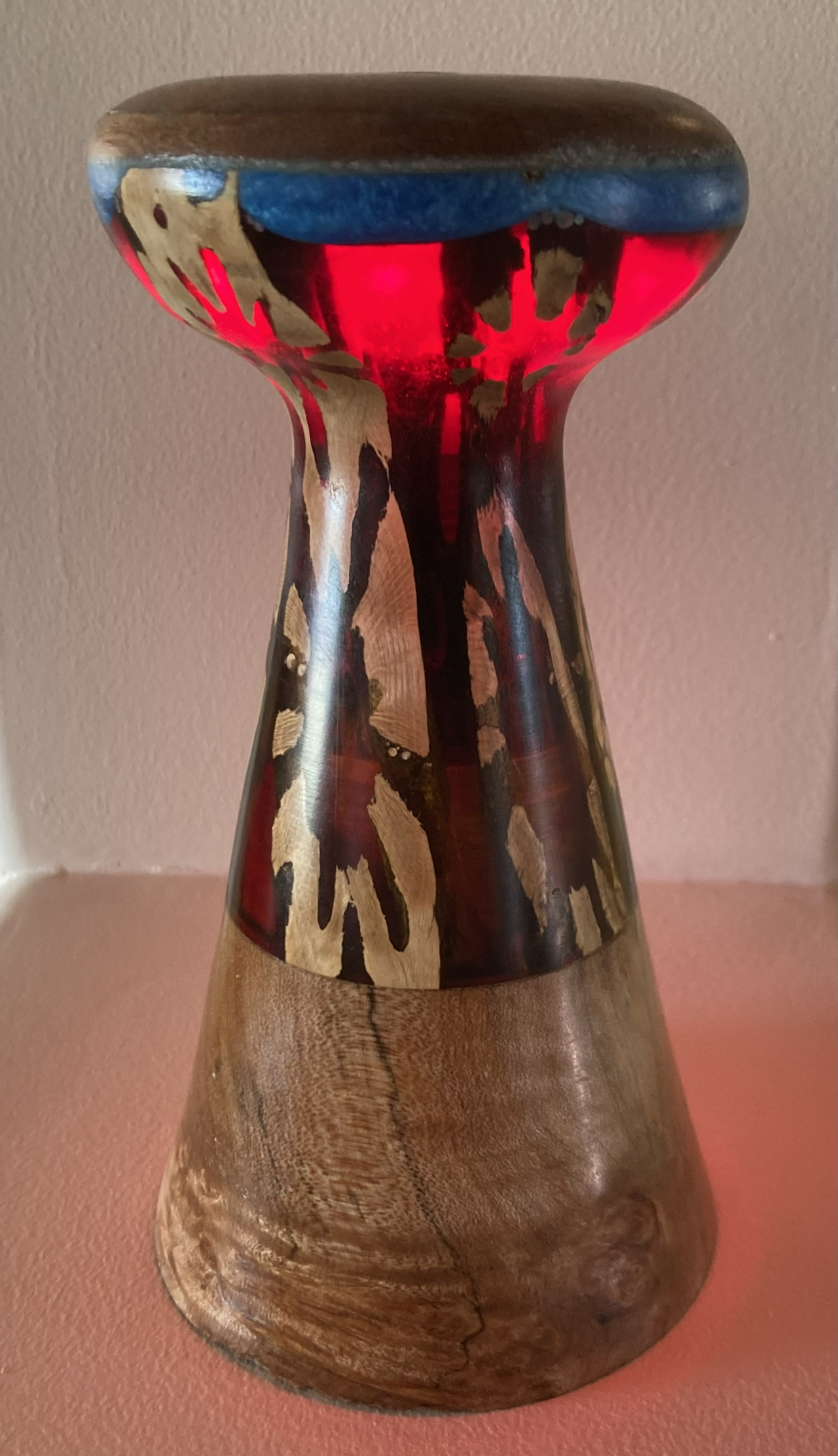
I made another touch control nightlight over the course of the past few months. The body is cholla and resin. The base is birch, and the top is sapele. It’s a nice red glow at its brightest, and barely noticeable at its dimmest, but it will last for over 80 hours on a charge at that brightness.
Read more...
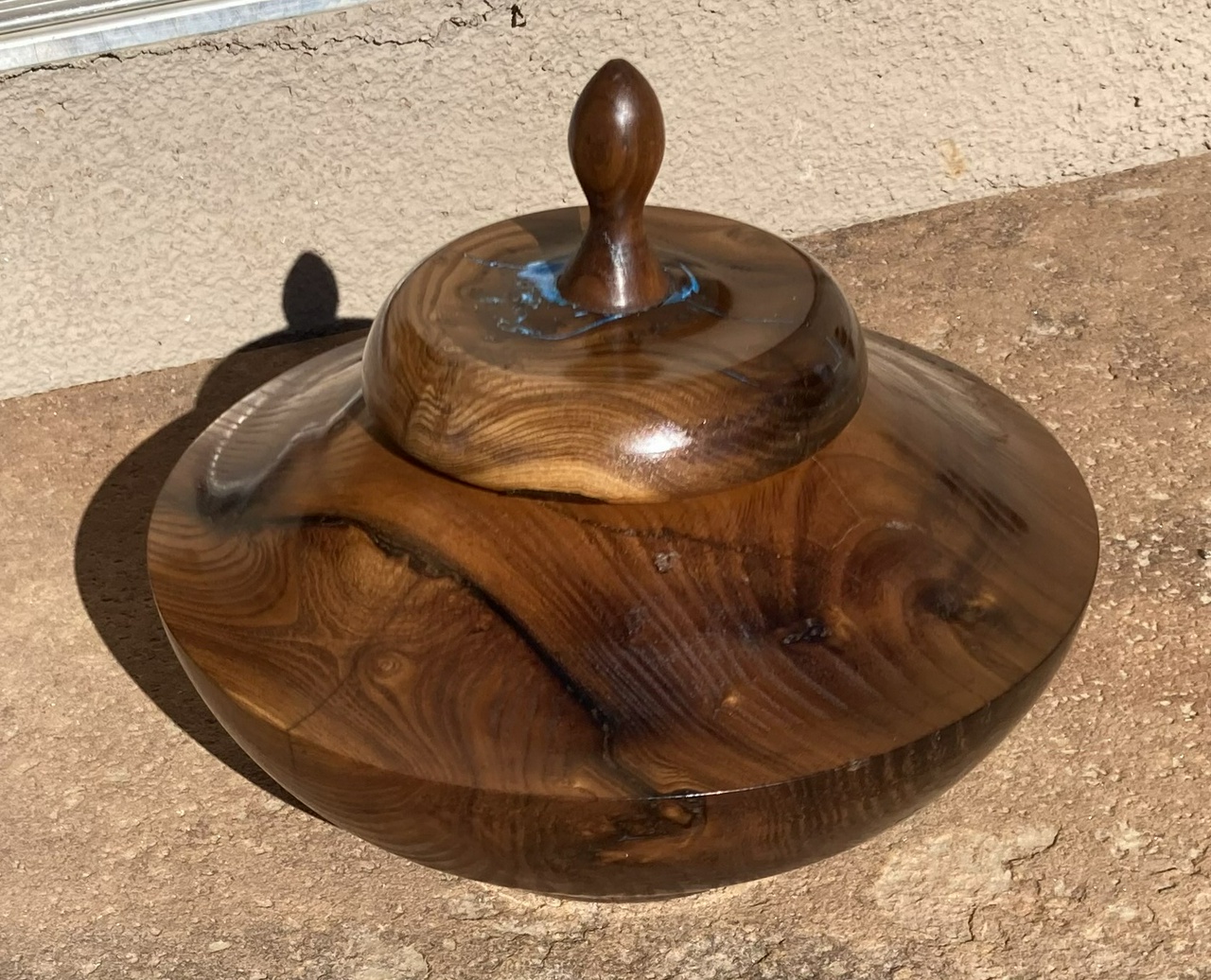
Got some Russian olive from a friend last Saturday. This bowl came out of one of the pieces. There are two cracks that wanted to come apart as I was turning it, and the shape was largely dictated by another crack that did come apart (and which put a dent in the ceiling of my shop).
Read more...
I've been wanting to learn more about bookbinding for a while, so when a Surprise Swap came up on Craftisian, I decided part of the build would be a box built with some bookbinding techniques.
Read more...
A small carved bowl made from Gambel Oak, from near Taos, NM.
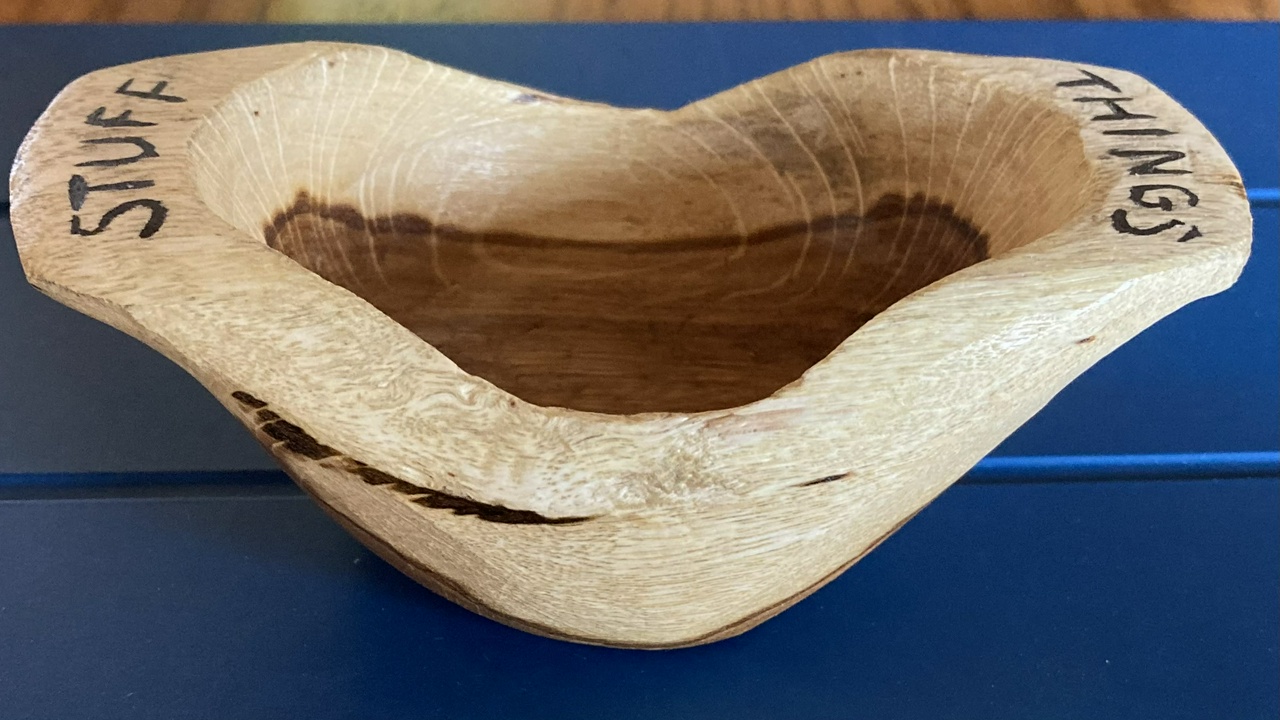
Read more...
On the first of the year, a friend gave me a couple chunks of chokecherry and a chunk of Gambel oak. I rough-turned the chokecherry into bowls in the first week of January, and finished turning this one in February.
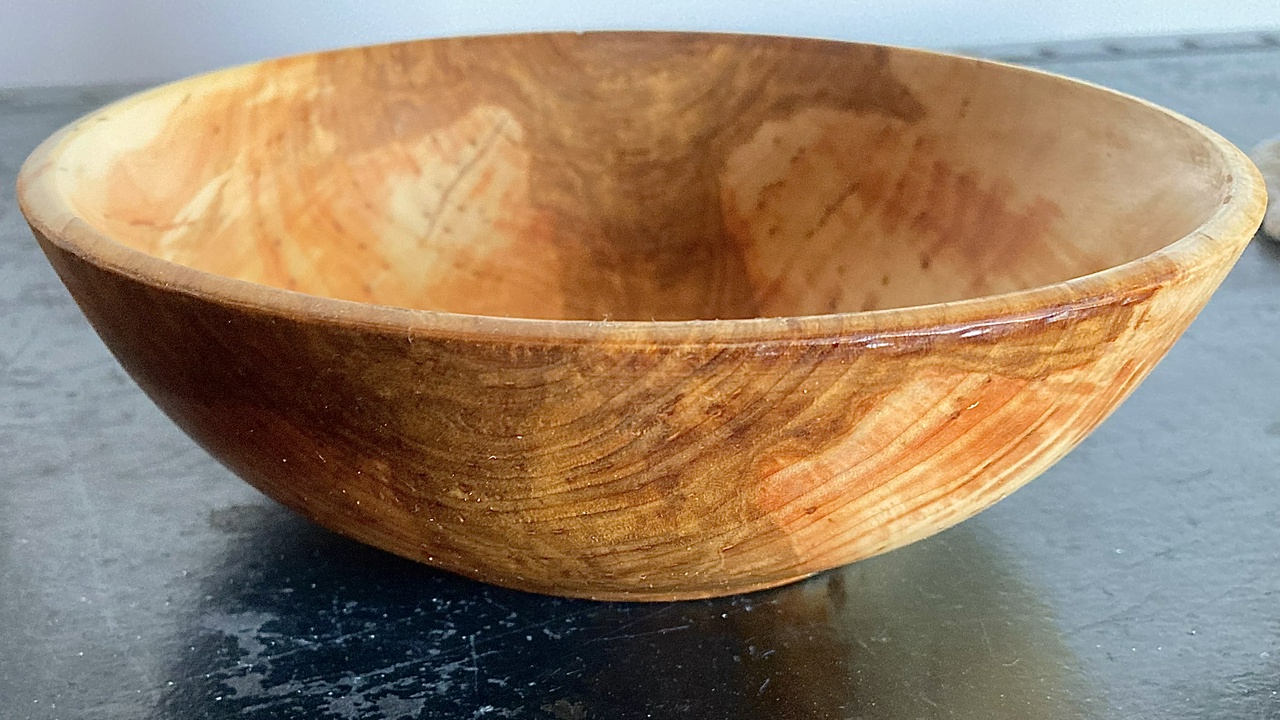
Read more...
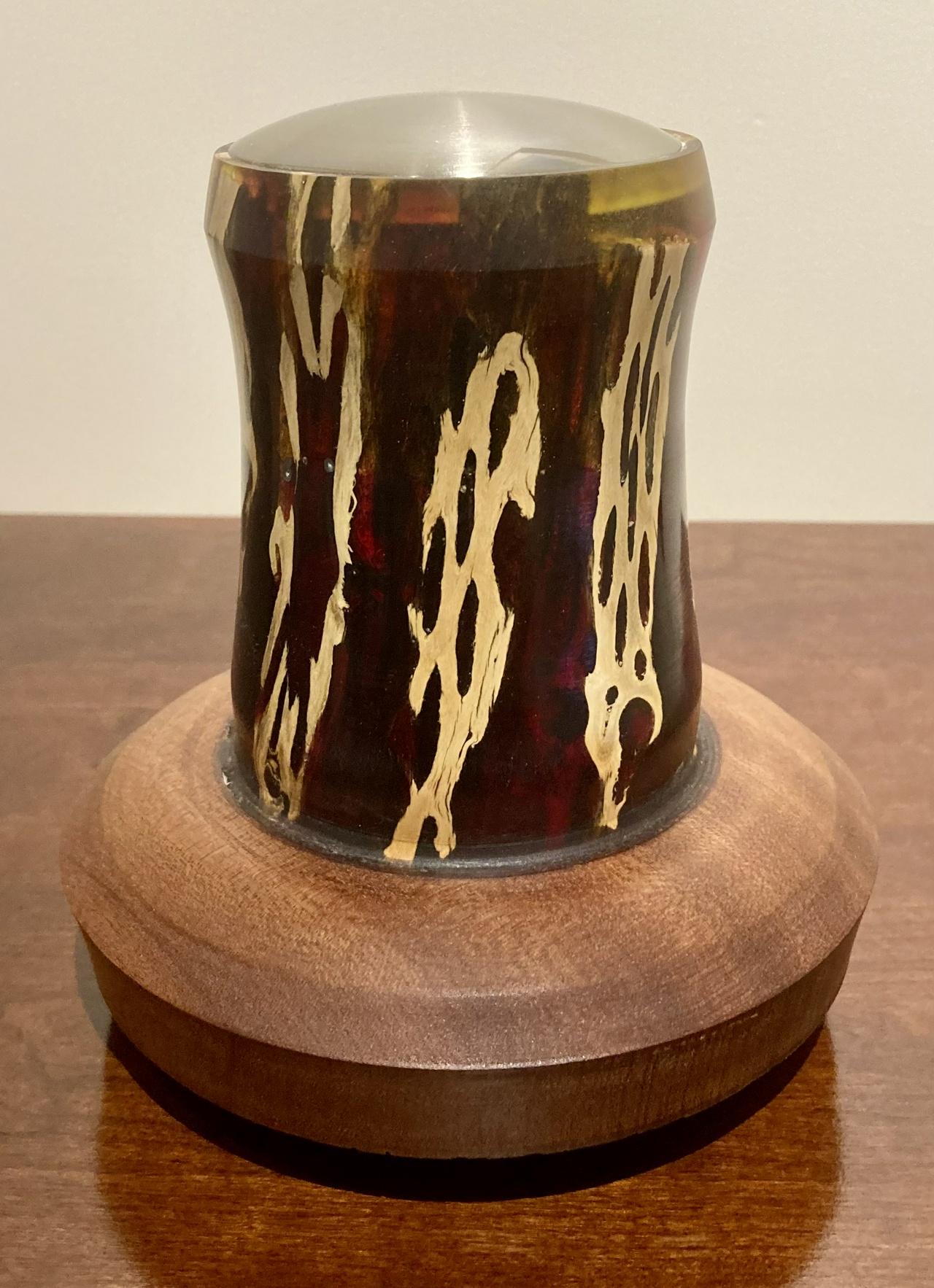
After making a couple bedside lamps, I wanted to make a version more suitable as a nightlight. This is the result, a lamp in which the LEDs shine through the resin, illuminating it from within. The light is a yellow glow that turns red farther down into the resin. Not perfect, because the hole in the resin for the batteries is slightly (less than a millimeter) too small, so the battery case is protruding a bit, but it’s usable, and I can always fix it later.
Read more...