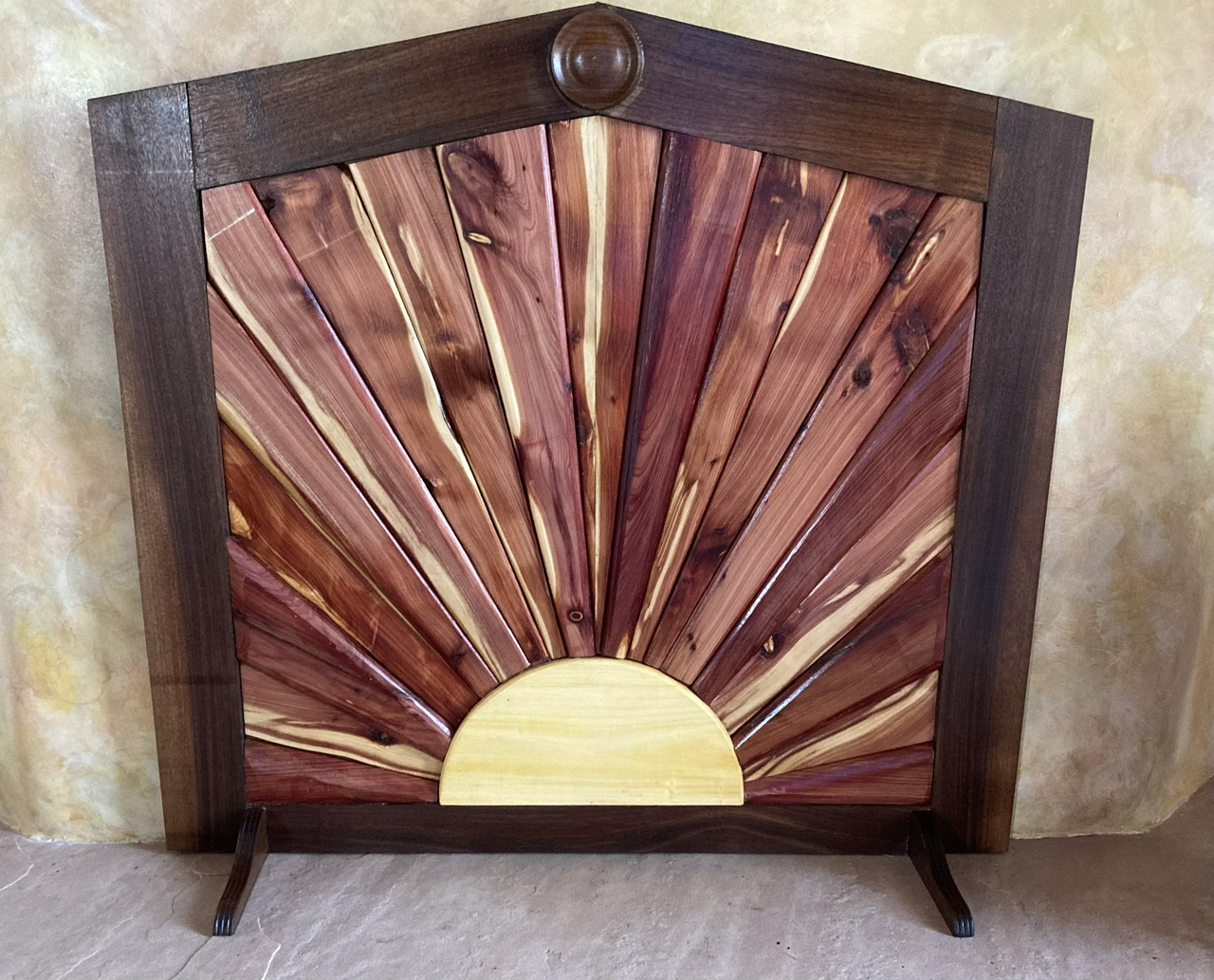
I built a screen for our fireplace recently, and am fairly happy with the result. The screen is for times when we’re not using the fireplace, since it looks dirty, and when the wind gusts, sometimes the damper blows open, and then we get a cold wind into the living room. This also greatly reduces the noise from wind blowing across the top of the chimney.
Read more...
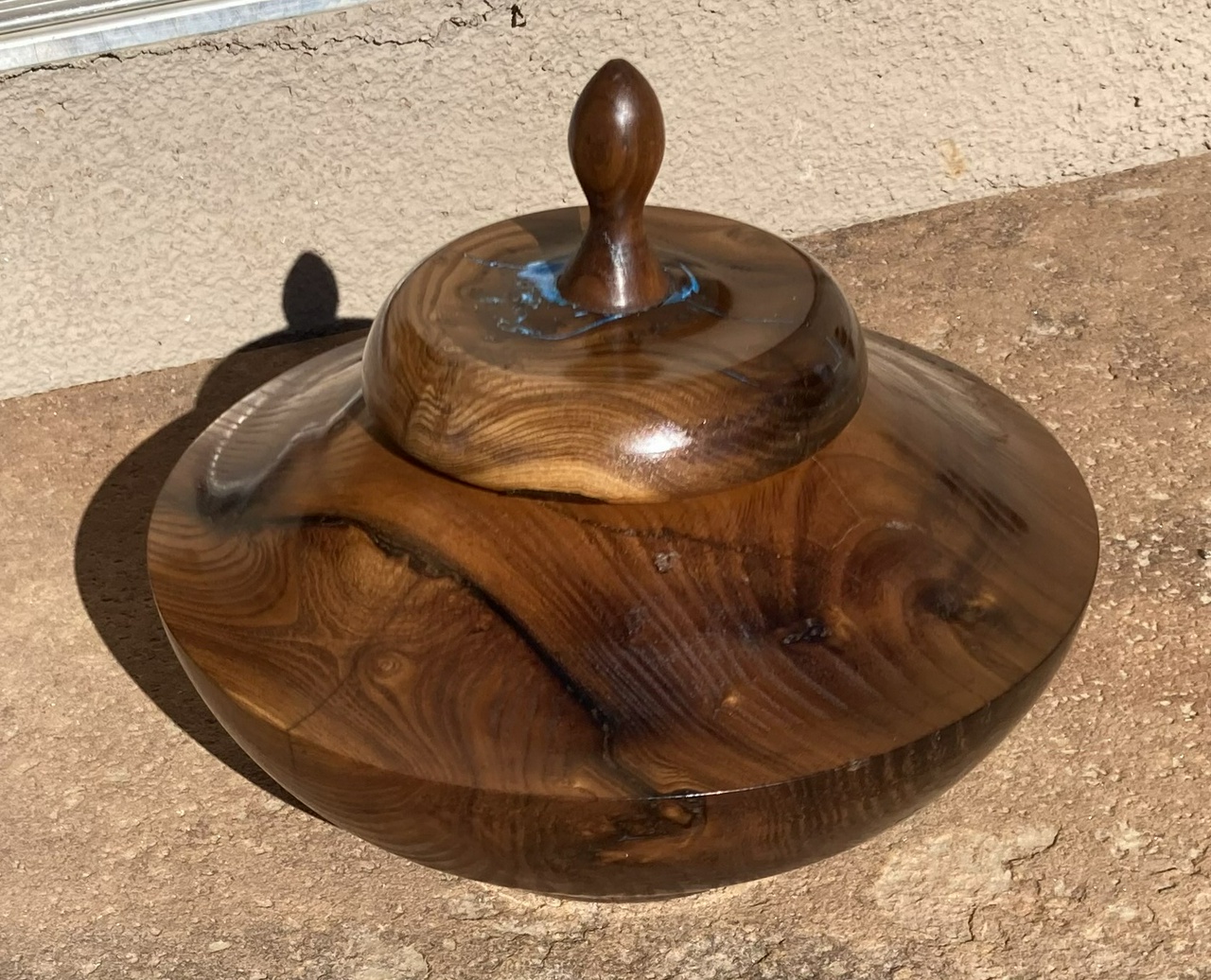
Got some Russian olive from a friend last Saturday. This bowl came out of one of the pieces. There are two cracks that wanted to come apart as I was turning it, and the shape was largely dictated by another crack that did come apart (and which put a dent in the ceiling of my shop).
Read more...
I've been wanting to learn more about bookbinding for a while, so when a Surprise Swap came up on Craftisian, I decided part of the build would be a box built with some bookbinding techniques.
Read more...
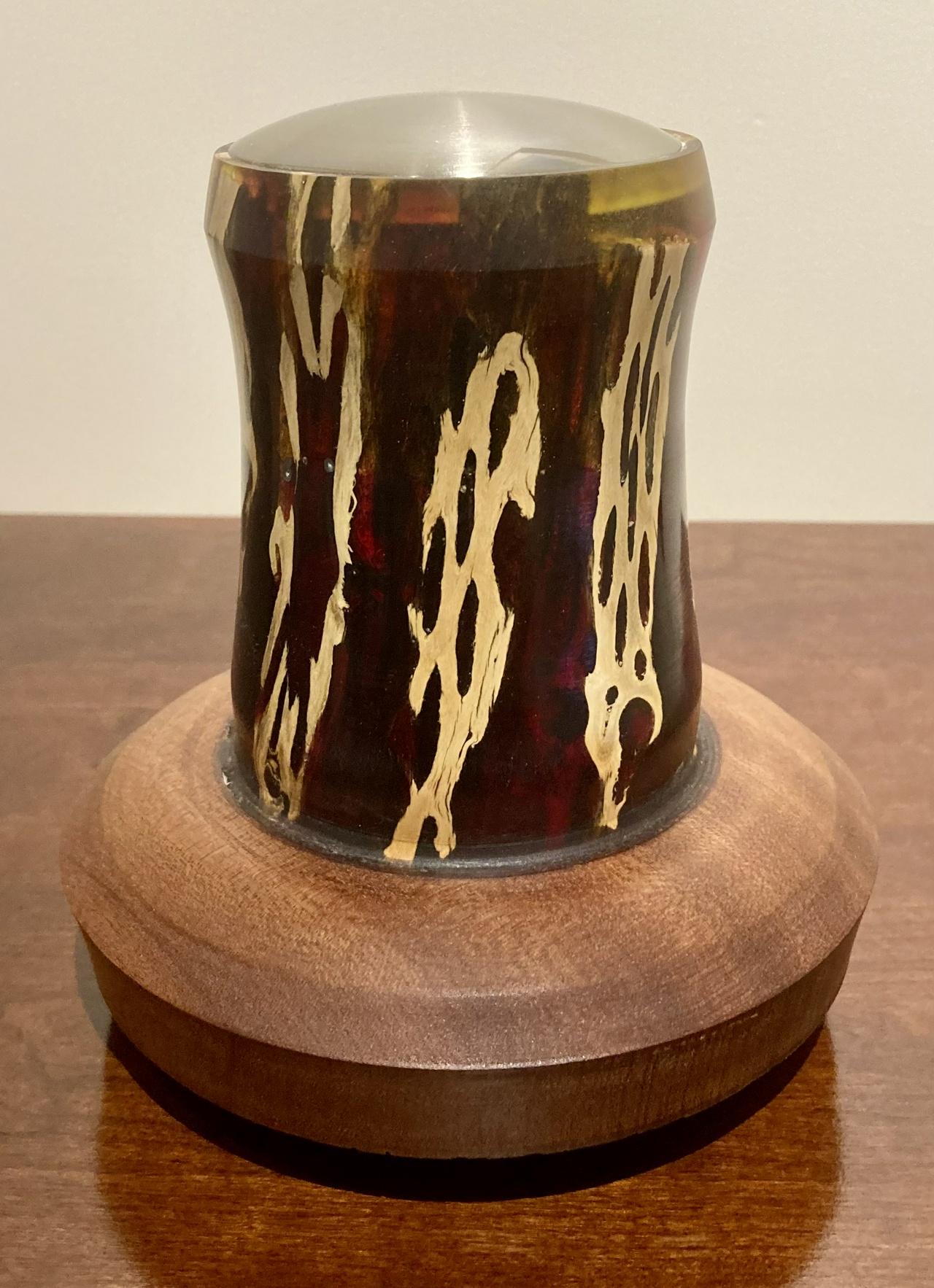
After making a couple bedside lamps, I wanted to make a version more suitable as a nightlight. This is the result, a lamp in which the LEDs shine through the resin, illuminating it from within. The light is a yellow glow that turns red farther down into the resin. Not perfect, because the hole in the resin for the batteries is slightly (less than a millimeter) too small, so the battery case is protruding a bit, but it’s usable, and I can always fix it later.
Read more...
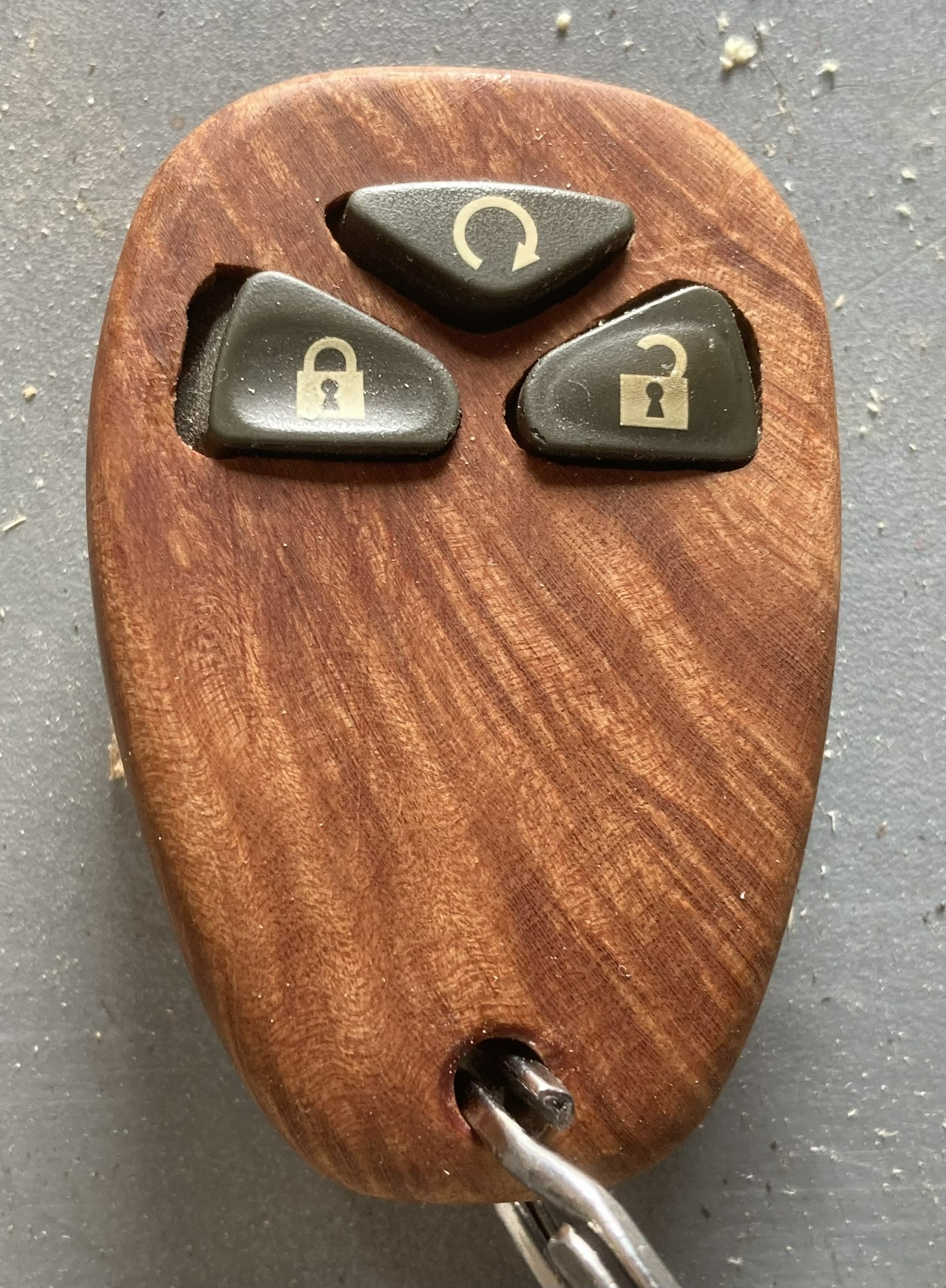
Recently, the remote fob for my truck cracked. The plastic case lasted about 14 years, and gave out pretty catastrophically. So I took it apart and looked at how the case was constructed and figured I could make one out of wood that would probably outlast the truck, which is getting some rust spots from its time in Minnesota.
Read more...